Fire retardant processing requests a skillfulness know-how of the compounding science:
- Recent studies pointed out that processing parameters during the transformation of the polymeric materials (injection moulding extrusion…)
Play a key rule on the fire properties - Major types of fire retardant need loading varying form 10 to 50% that lead the development of tailor made formulations. The shear stress and shear rate values generate thermo mechanical stresses that can degrade the polymer and modify its rheological behavior.
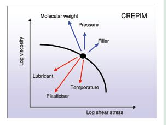
In order to guarantee your scale up phase and compatibility studies, CREPIM facilities a full range of material dedicated to polymer transformation: counter and corotative twin screw extruders, injection moulding machines, blenders dedicated to thermoplastic & rubber ,material…
A wide range of integrated solutions can be delivered to customer, including the purchase of the raw material, the compounding and performance assessment, and to the final scale up studies. The partnership that we propose to our partners guarantee a complete follow up of the formulation during the production launch and during the formula evolution
![]() |
Injection moulding machine
1 thermoplastic cylinder 1 cylinder for P.V.C with screw dedicated 1 Mould for the realization of standardized test specimen 150×20×4 mm and 100×100×3mm channel injector or radiated R10 injector. Mould and numerical controls ![]() |
![]() Characteristics: Closing force 500KN Screw diameter 35mm Max.injection weight 117g/ps Max.injection pressure 2500 bar Power engine of pump 18.5 KW |
Pressure measurement device is set up inside the mould to follow up in dynamic condition the molding conditions
Corotative twin screw extruder
![]() |
Characteristics: Segmented extrusion machine Corotative twin screw extruder Diameter of the screw O=25 mm Maximum length 16-48D Maximum Tº 450ºC Speed ran 0-150 rpm Output 1-20 kg/h Torque admissible 2×90 Nm Material all free flowing 2 feeding areas 1 degasification area |
Customization available with a full array of associated equipments: Liquid dosing system for reactive extrusion,Flat Die unit, Screw profile optimization
Conveyor line
![]() |
![]() |
Moulding machine
![]() |
To know more about our capabilities, feel free to e-mail us for information